Introduction
Most cement plants have a bank of storage silos to hold finished cement in inventory until required for packaging or bulk shipping. Storage silos allow cement plants to stockpile inventory until needed.
Buildups on the vessel walls can rob plants of the storage systems in which they have already invested. These buildups slow material flow and decrease the “live” capacity of the vessel.
Overcoming these flow problems and recovering storage capacity may require silo cleaning. Depending on how easily stored material compacts or hydrates, your silo may need to be completely emptied on a regular schedule as often as once a month or as little as every year. There are a number of ways to do this, but it is better to have an informed, safe approach.
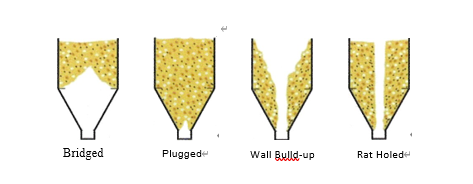
What needs to be noticed
First, cleaning a vessel from below should not be attempted. Poking from the bottom up inside the silo with a pole or pipe is asking for a large chunk of material to land on your head. Or the alternative, equally unsatisfactory, is to be buried under a mass of material that has suddenly broken free from the wall.
The safe way to clean out a storage vessel, both for plant personnel and for the structure, is to work down from the access opening(s) on the top of the structure. However, people should not be lowered into the silo through the opening(s) That is probably a violation of the confined space entry rules and is certainly a significant safety hazard. The work should be done from the top, but from outside of the vessel.
When working on top of a vessel, employees will need fall protection systems – safety belts and restraining harnesses, as required by OSHA in the US, and probably by other regional safety authorities.
It is important to remember that plant personnel will not be as comfortable with heights as they are on the ground. They do not have experience with fall protection systems and working at these heights, and may take risks or “shortcuts” that can lead to accidents. It may be wise to call in a specialist contractor, experienced with the nature and conditions of the job.
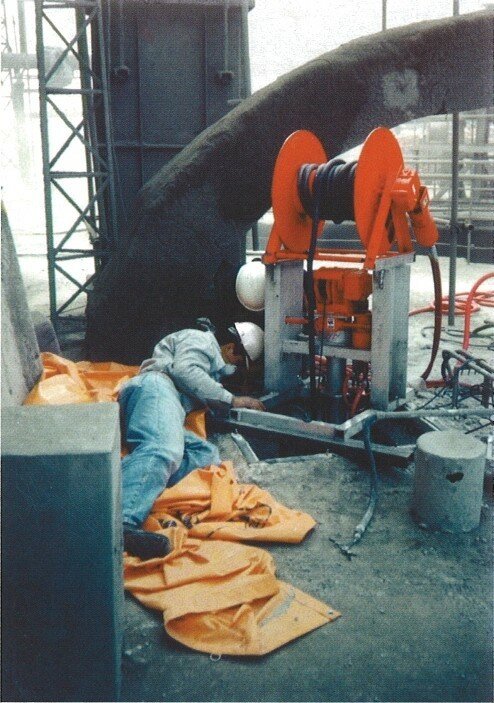
Any clean-out activity must be carefully controlled to avoid damage to the interior walls of the vessel, as this damage can reduce flow and cause continuing problems. Employees should not be sent into the vessel in a bosun’s seat and armed with a pick-axe; that is extremely unsafe for the employee and risks damage to the equipment.
It is important that the equipment has precise controls to manoeuvre the whip head and hold it in a cleaning position. The cleaning mechanism should not “bounce around” the inside of the vessel from side to side. This will not clean effectively; the cleaning head will not be focused on the material and there is a risk of damaging the bin walls or bottom.
It is also important that the operator is properly trained or, better still, experienced, with the skills to use the equipment properly.
Cleaning tool
It is desirable to have a cleaning method that can work inside the vessel, from the top of the vessel, but that can be controlled by personnel on the outside of the vessel.
If it is for a plant for which the customer does not foresee regular use of silo cleaning equipment, it probably makes better financial sense to employ a service firm that uses such equipment to clean the vessels.
There are several types of equipment that can be used for this purpose. One operates like an industrial-strength “weed whip”, rotating a set of “flails” against the material in the vessel. The cleaning head will typically be inserted through the access port down into the vessel on a pivoting arm. Ordinarily, the arm is 8 to 28 ft (2.4 to 8.5 m), allowing a cleaning radius of 56 ft. (in a straight line down from the access port). This equipment is usually air-powered by a compressor, with typical air consumption of 100 CFM at 85 PSI (2830 I/min at 5.9 bar)
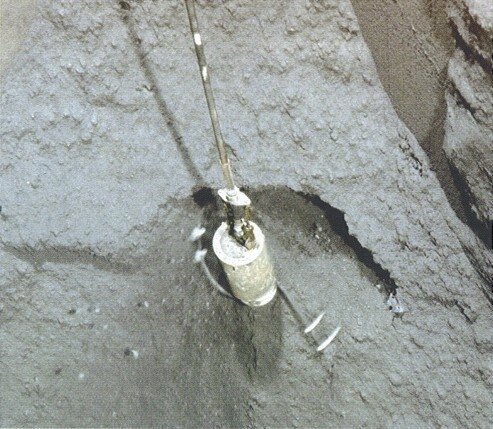
Whips and chains
The silo cleaning equipment uses its rotating “whips” to cut the material off the walls. One key to success is matching the flails to the material. Flails of a rubber-covered nylon rope have proven to work well in coal. These flails can be equipped with “knuckles” to improve the cleaning effect and extend whip life. The knuckles are typically made of urethane to provide impact without damage or sparks.
Steel chain is commonly used where Portland cement or any compacted material is involved where there is no risk of explosion. Non-sparking brass chain is often used on compacted materials where there is the risk of fire or explosion.
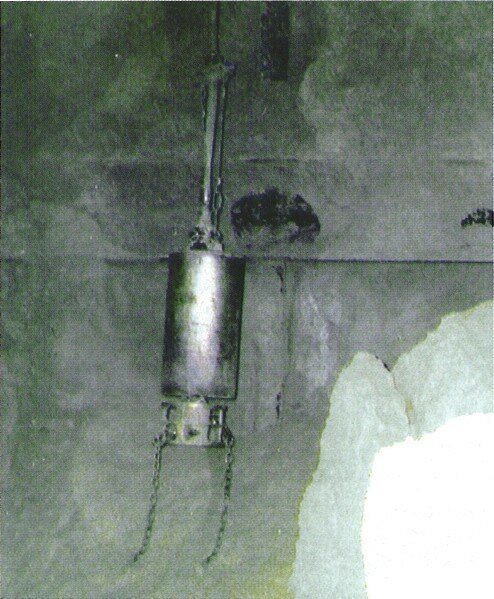
Cement silo cleaning procedure
Before starting the cleaning, it is important to ensure that there is a path for loosened material to leave the vessel. The discharge opening must be clear and there should be a takeaway mechanism at the bottom – a conveyor, a truck, or an end loader- so that large quantities of material are removed from the walls and the fallout does not build up below the discharge to the point where it blocks the opening.
When cleaning from the top of the vessel, one must start at the bottom of the buildup and work upwards. The wall accumulation is undercut until it falls by its own weight. When cleaning from the top, the removed material sits on top of the accumulation below it. The loosened material has no place to go until the entire mass is cut away and then the whole section will fall, risking damage to the bottom of the vessel or discharge.
This undercutting technique risks the occasional submerging of the whip head in removed material. Generally, the falling material will push the suspended cleaning head out of its way. If the cleaning head does become buried, one must wait for the material to feed itself out of the vessel, uncovering the whip head fi om the bottom.

How to deal with these problems when cleaning cement silos?
If the material is hung up or bridged to a “no flow” condition, the service provider will typically use a “bin drill” to open a 12 in. (305 mm) dia. hole through the material. This becomes a channel for the loosened material to flow through, and the silo cleaning crew then uses the bin whip to finish the cleaning.
If there are large chunks of material blocking the cone at the bottom of the vessel, a different solution is required. Here, the crew drills into the chunks and uses a blast to shatter the lumps into smaller pieces that can be worked out of the vessel discharge. The preferred method is to use a reaction of CO2 and an igniter. This is not an explosion and so there is no risk of fire or secondary explosion.
If a vessel is choked (that is, still running but nearly closed down), it will, in all probability, get worse. As material falls through the vessel, it will build up on the wall accumulations, gradually restricting the flow path until blockage is total.
As soon as a partial blockage is noticed, it may be wise to schedule a cleaning service. That will allow more time to work the cleaning into the plant operating calendar and the cleaning contractor’s schedule. It will also reduce the costs of mobilization charges and emergency plant outages. Customers will pay more for an emergency – “hurry up and do it because the plant is shut down” – silo cleaning than for a routine cleaning during a scheduled outage.
Longer term solutions
If the problem is recurring, it is probably time to consider improvements to the storage vessel. One thing that can be done is to note where the vessel hands up, in the valley angles, or in particular places on the walls. That provides ideas as to the type and placement of solutions that should be considered.
Perhaps a larger discharge opening would stabilize the flow rate without allowing material to accumulate, or a different bin bottom or feeding mechanism would allow the material to keep moving. Air cannons or vibrators, or some other method of material activation, could be installed to reduce the instances of buildup on the walls.
The benefits of silo cleaning
The cleanout of finished cement storage can bring several benefits to a cement plant. These include the recovery of material and storage capacity – both operating expenses that were paid for, but long considered missing and “off the books.”
At one cement plant, the silo cleaning crew cleared a silo in two weeks that had been out of use for 35 years. This added 3500 t of “live” storage capacity to the company.
At another plant, the cleaning crew was able to remove enough “lost” material (that had been written off the years) that the value of this recovered material paid the cost of the cleaning. In fact, the cement company made money on the sales of recovered material, in addition to the benefit of regaining its storage capacity.
In short, the cleaning of storage capacity can quickly turn into an economic benefit to an operation – an investment rather than an expense.
The costs of cleaning
Most cleaning projects are bid on a “time and materials” basis; it is difficult to give a firm estimate because the length of time can vary significantly depending on the amount and characteristics of the material in the vessel, some of those details cannot be determined until the cleaning has actually begun.
In general, an efficient silo cleaning crew can clean the walls in a 30 x 60 ft. (9 x 18 m) vessel, removing up to 150t of material/day (working time, excluding travel and setup).
It may be possible to reduce the mobilization charges for bringing a vessel cleaning contractor to a plant by scheduling a cleaning project in conjunction with other plants – other facilities that incorporate large bulk storage vessels – in the same geographic area. Or it may be possible to hold down the costs by allowing the cleaning service the option to schedule the cleaning at their convenience.
Maintenance of cement silo
To prevent stored cement from setting inside the silo, the structure must be completely watertight. Even pinhole leaks in silo roofs and walls damage your stored materials and can result in blockages and material flow issues. Ambient humidity levels can also cause some materials to set. If you do aerate stored materials, it is important to use air dryer systems to help lower the ambient humidity level in the silo. You should also avoid over aerating stored materials. Excess aeration can pump unneeded moist air into the silo which may lead to hydration of the cement.
Essential maintenance includes exterior waterproof coating(s) and keeping your air pad and air stones in good operating condition. Completely emptying your silo frequently is also important as it helps prevent compaction of stored materials.
Hung up, clogged, or slow running silos are a problem that will interfere with the efficiency and profitability of a plant. It is possible to keep materials flowing freely by removing buildups from silo walls with safe, effective and regular silo cleaning.