Stationary crusher is an important part of the crusher industry. It does not refer to a specific type of crusher, but is a general term for many crushers. After we published an article about mobile crushers last time, many readers left a message asking if there are mobile crushers, are there any stationary crushers? No, the stationary crusher is here. I hope you can have an understanding of the stationary crusher after reading this article.

What is a stationary crusher?
The stationary crusher is mainly developed for mine crushing and sand making, and is a general term for a commonly used crushing equipment. Although there are many traditional crushing equipment, stationary crushers are also advancing with the times. For example, stationary hydraulic crushers are innovatively developed. After the equipment comes out, it solves the ore crushing needs of sand and gravel aggregate enterprises, metallurgical foundry enterprises, crushing plants, cement mines, and metal mines.

The stationary crusher can crush large pieces of ore into small pieces, which are convenient for transportation, and can work continuously in complex work sites, which reduces the work intensity of workers and improves work efficiency. At the same time, the stationary crusher can also achieve fine crushing and increase the output.
What working scenarios are the stationary crushers mainly used for?
A stationary crusher is not a crusher, so it is common to use multiple crusher types in a project and combine them to meet the crushing requirements. This combination of various fixed crushers is also called a fixed crushing station, which can meet a variety of crushing requirements, such as the following requirements:

Primary crushing
As the first stage in the crushing stage after the material is withdrawn from the mine, the purpose of primary crushing is to reduce the material to a size and size that can pass through secondary crushing. The minimum setting for most primary crushers is generally 4 to 6 inches, and jaw crushers, cone crushers, impact crushers and gyratory crushers can all meet these requirements. Although some of these crushers are also used for secondary crushing, they can also be used for primary crushing as long as they are properly sized.
Secondary crushing
In secondary crushing, the reduction ratio is an important consideration. This requires knowing your final output and the feed requirements of the tertiary or final reduction crushing station to determine how much reduction is required at this stage. The cone crusher is a commonly used secondary crushing device because of its versatility in terms of feeding, closed setting, speed and throwing.
Three, Four, Final reduction and crushing
At this stage, the size of the rock or other materials is shaped into a saleable product, so at this stage, whichever crusher modifies the shape and size of the product to meet the customer’s requirements, which type of crusher is used, there is no fixed requirement. , mainly depends on the demand.
What are the advantages and disadvantages of stationary crushers?
The stationary crusher is a kind of equipment relative to the mobile crusher. The stationary crusher is the crusher fixed on the site, and the mobile crusher is the movable crushing equipment. The two have their own advantages and disadvantages. The advantages of the crusher have been mentioned in the previous article. Now let’s talk about the advantages and disadvantages of the stationary crusher:

Advantage
Wide range of applications
The application range of stationary crushers is relatively wide, which is mainly reflected in the wide application fields of stationary crushers and the variety of materials that can be processed. Common application fields include construction, mining, power plants, chemical industry, metallurgy, cement, roads, sand and gravel plants, dry mortar, concrete aggregates and construction waste; the materials that can be processed are iron ore, gold ore, copper ore, Cobblestone, granite, limestone, basalt, steel slag, construction waste, etc.
Various models
Stationary crushers include jaw crushers, cone crushers, and impact crushers. These different types of production equipment include different series and models, which makes stationary crusher equipment more models, giving customers more The choice space can also better meet different production needs.
Excellent performance
The excellent performance of the stationary crusher is mainly reflected in the good stability and high reliability of the model, and it is not easy to fail when processing materials, and the main parts of the machine use production materials with high pressure resistance and wear resistance. , so the service life of the machine is relatively long. In addition, the structure of the stationary crusher has been continuously optimized, so both production and operation are more convenient. Even if there is a fault, the machine will be repaired in a very short time. , greatly reducing maintenance time and maintenance costs.
Shortcoming
For the stationary crusher, its biggest disadvantage is that it cannot move freely. For the processing of materials, the machine must be fixed first, which makes the materials need to be transported before they can be processed, which results in material transportation. The increase in cost increases the production cost, and because it needs to be installed in advance, the machine cannot be produced directly, which will also increase the cost to a certain extent.
What are the components of the stationary crusher?
The equipment used in the stationary crushed stone production line is stationary crushers, which are suitable for stone plants with relatively fixed sites and large crushing sites. Stationary crushed stone production lines require all equipment to be piled, fixed, installed and then connected. A complete set of fixed crushing production line is mainly composed of feeding equipment, crushing equipment, screening equipment, sand making equipment, storage and transportation equipment and dust removal equipment.

Stationary crushing production line equipment:
Feeding equipment
The vibrating feeder can continuously feed the material into the crusher evenly and quantitatively, and has the characteristics of stable vibration, uniform feeding and low cost.
Crushing equipment
The jaw crusher is mainly used for the primary crushing of materials and has good versatility. It has the characteristics of high efficiency, large output and simple maintenance. Cone crusher and impact crusher are commonly used crushing equipment. Cone crusher and impact crusher are often used for fine crushing. Cone type is suitable for materials with moderate hardness or above, and impact type is more suitable for soft materials.
Screening equipment
The screening of the crushing production line can be used for both pre-screening and inspection screening. The most commonly used screening equipment is a circular vibrating screen. The circular vibrating screen has a variety of screening specifications. It has high screening efficiency, The advantages of low pollution and durability.
Sand making equipment
Sand making machines are used to make commercial sand, relying on the principles of “stone hitting stone” and “stone hitting iron”, and have a good shaping effect. The operation is simple, the output is high, the particle size is generally cubic, and the fineness is uniform. For example, the vertical shaft impact sand making machine is a relatively popular sand making machine on the market.
Storage and transport equipment
Storage and transportation equipment includes silos and belt conveyors. The belt conveyor has the characteristics of continuous conveying, long conveying distance and large conveying capacity.
Dust removal equipment
The dust removal equipment mainly includes fans, dust treatment and recovery systems. In addition, the sand aggregate production line should also be equipped with sand washing machine, dryer, electronic control system, and dust removal system equipment. The common configuration scheme of fixed crusher production line is:
According to the configuration of the processing material
Handling medium hardness and soft materials (such as limestone, feldspar): feeder + jaw crusher + impact crusher + vibrating screen + conveyor.
Handling hard materials (such as pebbles, basalt, granite): feeder + jaw crusher + cone crusher + vibrating screen + conveyor.
Handling brittle materials (such as coal, coal gangue): feeder + hammer crusher + vibrating screen + conveyor.
Configured according to production
It is suitable for output below 50 tons per hour: feeder + jaw crusher + compound crusher/pair roller crusher/double-stage crusher + vibrating screen + conveyor.
Suitable for output from 50 to 300 tons per hour: Feeder + Jaw Crusher + Cone Crusher / Impact Crusher + Sand Washer + Vibrating Screen + Conveyor.
Feeder + Hammer Crusher + Impact Crusher + Sand Washer + Vibrating Screen + Conveyor.
Applicable to the output of more than 300 tons per hour: feeder + jaw crusher + cone crusher + impact crusher + sand washing machine + vibrating screen + conveyor.
What is the difference between a stationary crusher and a mobile crusher?

Stationary crusher:It needs to be installed on a fixed site, and there is also a mixed territory for infrastructure construction. The installation of the entire production line has relatively high requirements on the site, and the processed materials need to be transported to the vicinity of the production line. The configuration of the entire production line is relatively fixed. If the raw materials processed or the production capacity requirements change, the entire production line may not be able to adjust in time.
Mobile crusher: It has less requirements on the site and can choose various sites. In essence, various equipments are placed on a vehicle, and the equipment on the vehicle can be independently selected and changed. If the production materials and production requirements change , can also be changed at any time.
Which is better, stationary crusher or mobile crusher?
The mobile crusher is a newly emerging crushing equipment. It is more popular in the current market because it can move freely and can change the combination of equipment as the demand changes, so as to meet the production requirements. However, as a traditional crushing equipment, the stationary crusher still occupies the mainstream of the current market. This is not a temporary substitute, and in some specific occasions, the stationary crusher is more suitable. Therefore, these two types of equipment have their own advantages and should be selected according to their own needs.
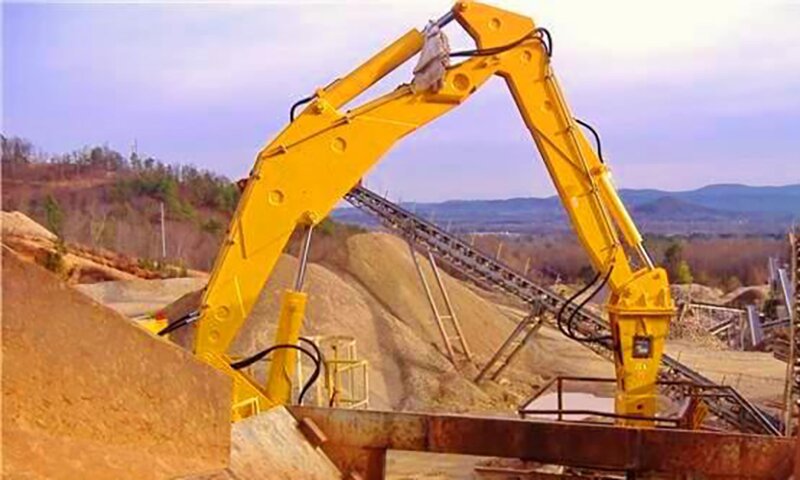
That’s all for the introduction of stationary crushers. Do you have enough knowledge about stationary crushers now? If you still have questions, you can leave a comment and we will reply to your questions one by one. At the same time, I hope you can continue to read other articles on this site, thank you for your attention.